Why volumetric technologies for your product line?
There are several options you could use for your food product filling line, but volumetric technologies are undoubtedly the best. Volumetric fillers provide three simple but powerful benefits that will elevate the efficiency of your production line: they are faster, more cost-effective, and easier to use than any of the alternatives.
The three benefits of volumetric fillers
The following three benefits make volumetric fillers the perfect choice for the ready-made meal industry:
- Speed: With volumetric filling machines, your filling cycle typically gets faster than it was before. There is no substantial pause between fills, which means the production line runs smoothly and continuously. In fact, our machines can fill up to two containers per second, depending on the model you’re using and the kind of food being dispensed.
- Lower costs: Volumetric filling is cheaper than gravimetric filling because it requires less machinery and electronics, and works faster. You can thus keep your production costs under control.
- Ease of use: Volumetric fillers are simply easier to use. They are easily programmed using the programmable logic controller (PLC) system, and changeovers are fast and straightforward.
Our innovative filling machine systems
Multi-Fill supplies several innovative volumetric filling systems to the ready-meal industry. Each of them provides these three benefits according to the needs of your system. They include the following:
- The MPFMP-060 is a volumetric filler ideally suited for lower speed production lines, research and development labs, and pilot plant operations. The product is loaded on to the top pan and manually fed to the filling tube by an operator.
- The MPFSH-075 fills 60 to 75 containers per minute. It can be upgraded to an MPFSC-120 for increased speed and/or different products at a later date. The MPFSH-075 is recommended for applications where more automatic product feeding is required. It is suitable for lower speeds, easier (looser) products, and smaller fill weights.
- The MPFSC-120 is our high-speed machine, which fills up to 120 containers per minute. It is recommended where not only more automatic feeding of the product is required, but also where the capability for higher speeds, stickier products, or larger volumes are needed.
For more information on top-of-the-line volumetric fillers for your production line, contact us here.
Designing a food filling line: Product is king

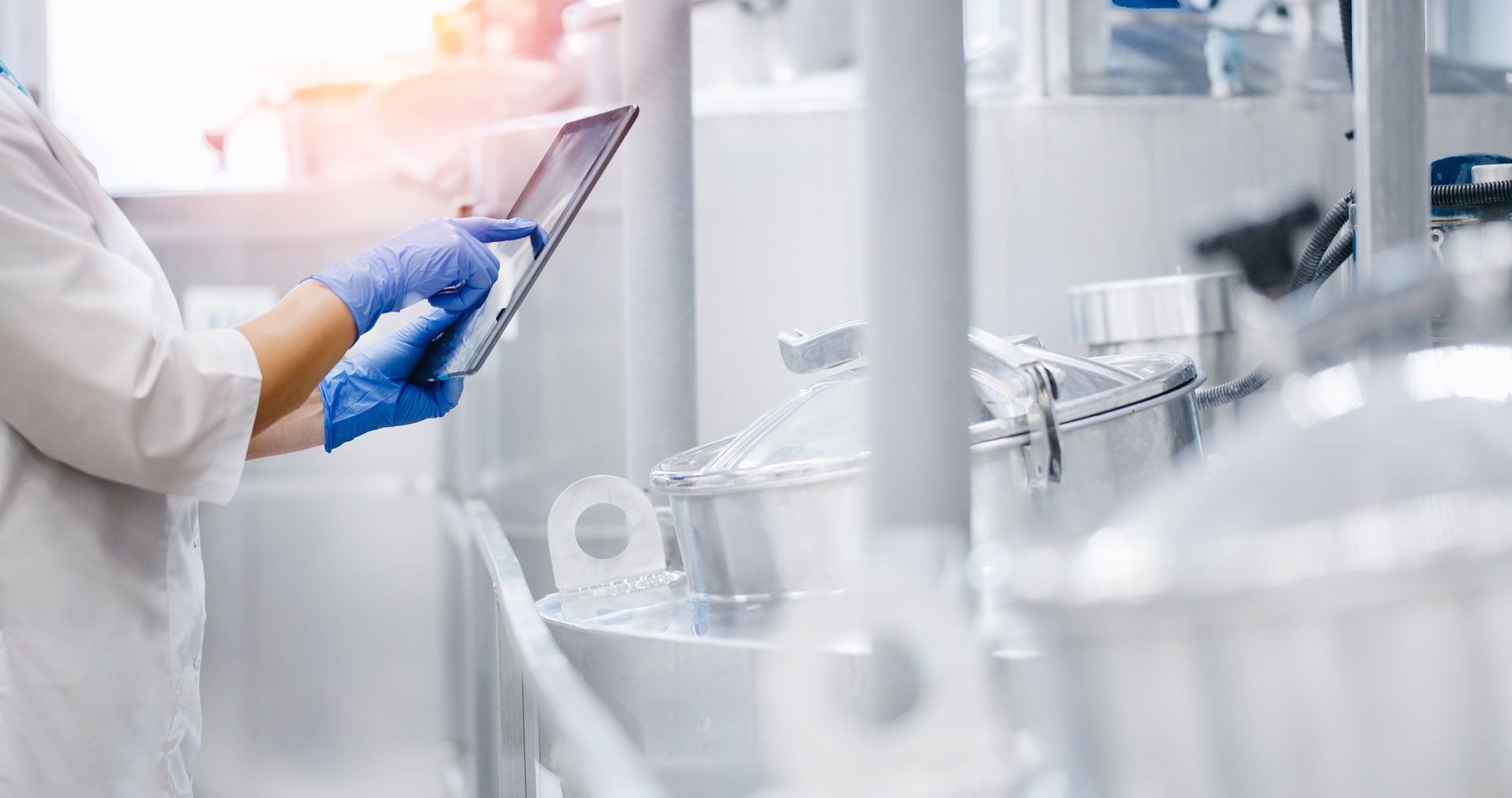
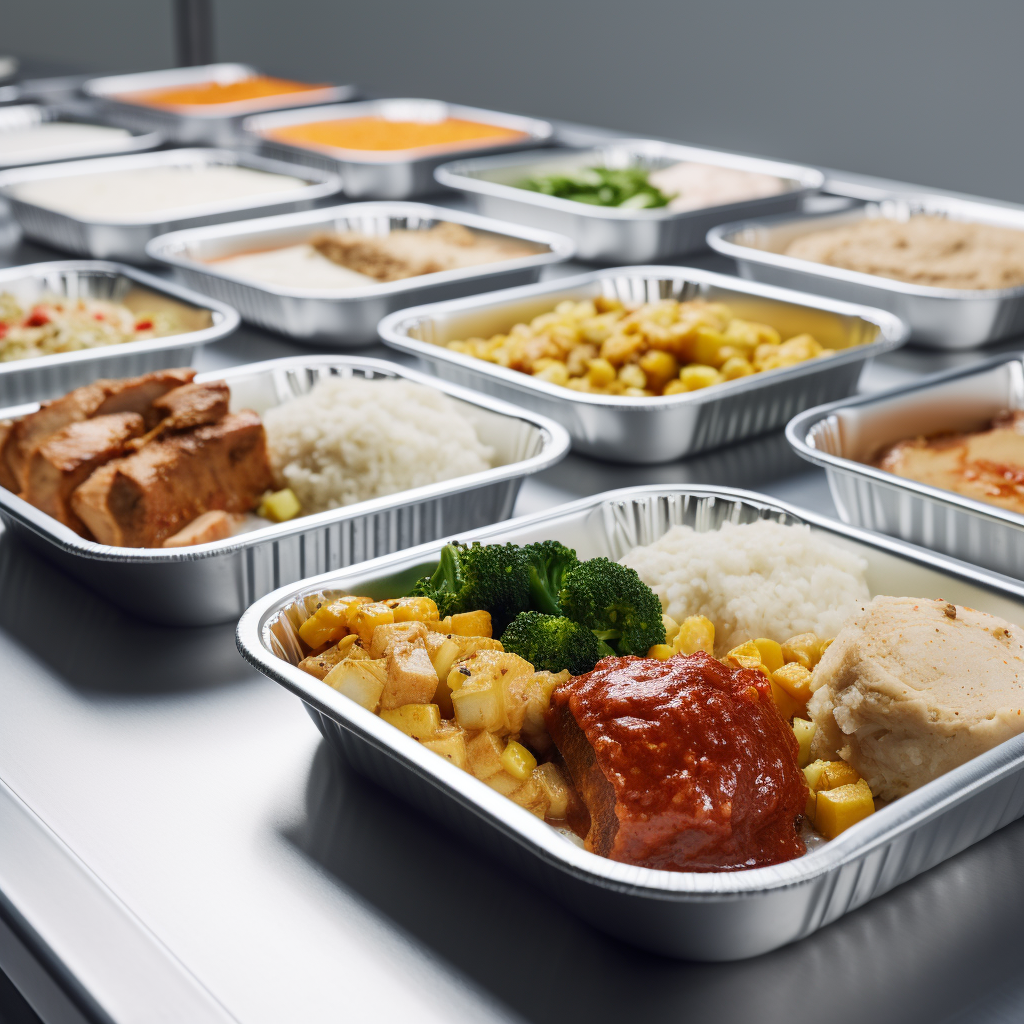