Understanding volumetric filling machines
Volumetric filling machines are used to deposit specific product portions into packaging materials such as containers, packets and the like. Focused on hygiene, accuracy and efficiency, these machines can improve your packaging processes substantially. Read on to find out more from Multifill, providers of high-quality food filling systems.
The different uses of a filling machine
The basic use of a filling machine is to measure a product from bulk and fill it into a container, bag, bottle or other packaging materials. These machines are used across sectors in industries specializing in commercial applications. There are several types of filling machines that perform specific functions. These include:
- Liquid filling machine: Also known as a flow filling machine, these filling machines are primarily used in beverage-related industries. They can dispense the finished product such as alcohol, soda or water into cans, bottles, cups or other containers.
- Powder filling machine: This machine uses spiral feeding to dispense free-flowing and non-free-flowing products such as salt or sugar into containers.
- Vibratory weigh filling machine: Used for filling dry granular products, this machine consists of several vibrating trays that drop the product onto a weigh bucket. Once the bucket is filled with a predetermined weight, it dispenses the product into a container.
- Capsule filling machine: This machine is ideal for the pharmaceutical industry to dispense capsules, tablets and pills.
- Positive displacement pump filling machine: These machines are perfect to dispense high-viscosity liquids including lotions and gels or heavy-paste products such as hair conditioners or shampoos.

Streamline your business with a vegetable filling machine
Investing in a vegetable filling machine can be highly beneficial for your business as it makes the production and packaging line more efficient. It is also gentle on the finished products and prevents issues such as wilting or water loss in vegetables. The addition of such a machine at your premises provides you with a competitive edge over other businesses that do not.
Benefits of using a rice filler
Finding an automated filler for the packaging of granular products such as rice can streamline your packaging operations substantially. Read on to find out how.
- As a core function, rice filling machines fill raw rice into bags, pouches or containers as in prescribed weights. These can be filled in pre-determined quantities accurately, preventing the discrepancies that arise with manual filling.
- Once the rice filling machine completes the filling process, it seals the container or bag to prevent contamination from external factors. It is for this reason retailers always advise customers to never purchase products if the packaging is broken or tampered with.
- When rice is exposed to air over a period of time, its taste and quality are reduced drastically. However, when it is packaged using a rice filling machine, it stays fresh longer without the need for preservatives or chemicals.
- Production and packaging operations are more efficient with the use of rice filling machines as there is minimal manual labor involved.
- A food-related business must comply with several regulatory and standard rules and regulations related to accuracy and safety while packaging its products. Using a rice filling machine can reduce the incidence of errors or discrepancies ensuring all packages weigh the same and are identical.
- A rice filling machine, along with vacuum packaging, increases the shelf life of the finished product as its airtight nature prevents the growth of microorganisms or harmful bacteria.
Benefits of using a vegetable filler
- Utilizing manual labor to fill in containers is a time-consuming and tedious job. However, using a vegetable filling machine increases throughput and productivity without the need for manual intervention.
- There is more consistency in packaging, grading and sorting of the vegetables using automated filling machines. These machines have the capability to detect defects in vegetables that help sort them efficiently. These machines also reduce discrepancies in the weight and amount of the finished products as the quantities are automated and predetermined. This ensures consistency in the look and feel of your finished product.
- Manually sorting vegetables can result in a wastage or subjective elements that lead to crop waste. However, with the use of vegetable filling machines, the food products are packaged with minimal wastage and bruising.
- Vegetable filling machines save time and money as they have the capability to fill multiple containers simultaneously. The margin for error is also substantially reduced as there is no human intervention during the packaging process.
- Using vegetable filling machines also keeps the finished food product safer to consume as the incidence of contamination is reduced.
At Multifill, we have three main filling machines that can sort, grade and package your vegetables:
- The MPFMP-060: This filling machine is suitable for smaller businesses that do not have huge outputs or plans of expansion. These machines can fill 50 to 60 containers with vegetables in one minute.
- The MPFSH-075: Suitable for lower speeds and loose powdery products, this filling machine packages 60 to 75 containers in a minute. It can also be upgraded if larger volumes are required.
- The MPFSC-120: This filling machine provides the highest speed as it can fill up to 120 containers in a minute.
Do I need volumetric filling machines for a successful business
Using a volumetric filler can help your business with cost savings, better sorting and packaging capabilities, making your operations more streamlined and efficient.
- Speed: With quicker fill cycle times, volumetric fillers complete the packaging process much faster than other machines or manual filling.
- Cost: Volumetric fillers are more cost-effective than net weight fillers and provide you with more accurate filling.
There are several types of volumetric filling machines that you can choose from in order to help your business. A start-up or small business may require an entry-level machine, while medium to larger businesses would benefit from larger filling machines. These are:
Manual fillers: Perfect for home-based or small businesses, these fillers have lower production rates.
Semi-automatic fillers: With greater production rates than their manual counterparts, these machines are a perfect fit for small businesses that are looking to expand. They still require some level of manual intervention and are considered an affordable, efficient and smart option.
Automatic fillers: If you have a large-scale business, automatic fillers can meet the high production rates you need. They are equipped with conveyors and belts that reduce the need for manual intervention. However, these machines are much more expensive and require regular maintenance as well.
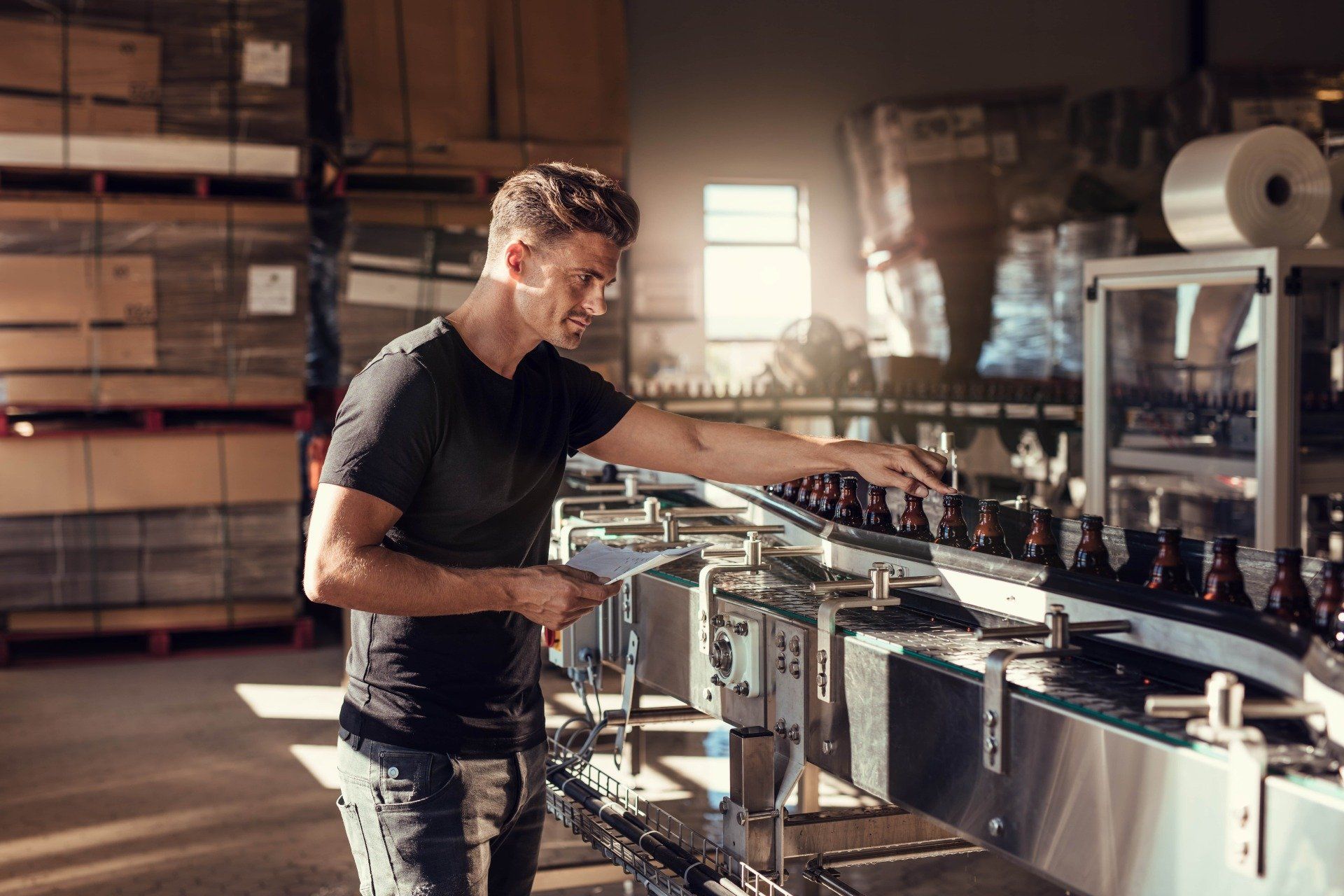
Tips for maintaining vegetable filling machines
Taking care of your vegetable filling machines ensures it works efficiently for years to come. Follow these tips from Multifill.
- Preventative maintenance schedule: As is the case with other heavy machinery, it is important to conduct preventive maintenance periodically to recognize any issues that need to be amended. It is also recommended to carry out preventive maintenance tasks such as the lubrication of various components to reduce the incidence of damage, both minor and major.
- Spare parts list: When you purchase a vegetable filling machine, always ensure you receive a spare parts list including high-wear, medium-wear and low-wear parts. Always keep high-wear parts in stock at your premises as they may take longer to be shipped from the manufacturer, leading to production downtime.
- Upgrades and obsolescence: Vegetable filling machines, as with other automated and electronic machines, are upgraded with newer technology and parts constantly. It is recommended to keep in contact with your manufacturer and request them to notify you of any upgrades.
Are prepared salads as fresh
With the advent of social media and information at everyone’s fingertips, there is a lot of talk about the importance of hygiene of prepared food items, especially salads and fresh vegetables. Food and beverage businesses have a huge responsibility to ensure their food is free of bacteria and contamination for the health of the customers. This is the reason why high-quality and efficient vegetable or volumetric filling machines are important. These machines are known to package prepared salads safely and hygienically, maintaining the look and appeal of the finished product as well.

Pros and cons of prepared salads
As consumers, we are sure you want to know how healthy prepared and packaged salads are. Multifill outlines the pros and cons of prepared salads:
Pros of prepared salads
- The primary advantage of prepared salads is the health benefits they offer to consumers. They also offer a high level of convenience for customers as they are easily available with a variety of choices in terms of vegetables, fruits and dressings. Therefore, if you are in a hurry, opening up a bag of leafy greens and pouring a delicious dressing can be the way to go.
- Prepared or frozen meals found in supermarkets and grocery stores are generally high in starch and salt. They are also usually devoid of vegetables and other healthy additions. In such situations, choosing a bag of prepared salad over these unhealthy choices can go a long way.
Cons of prepared salads
- Once vegetables are harvested, they lose a percentage of their nutritional value. It is safe to assume that prepared salads take longer to reach the consumer and may lose even more nutrients in the process. It is said that leafy greens may lose a gram of nutrients every hour.
- Once prepared and packaged, the salad, especially the leafy greens, must be stored in a controlled cold environment. If this is not done properly at a supermarket or store, consumers could end up with prepared salads that could be risky to consume.
- It is recommended to always check the expiry or use-by date to avoid consuming old, spoilt salads. Remember, they may still look bright green and fresh, but they may not be safe to eat.
For more information on volumetric filling machines and how they streamline your business operations, contact Multifill today!
Designing a food filling line: Product is king

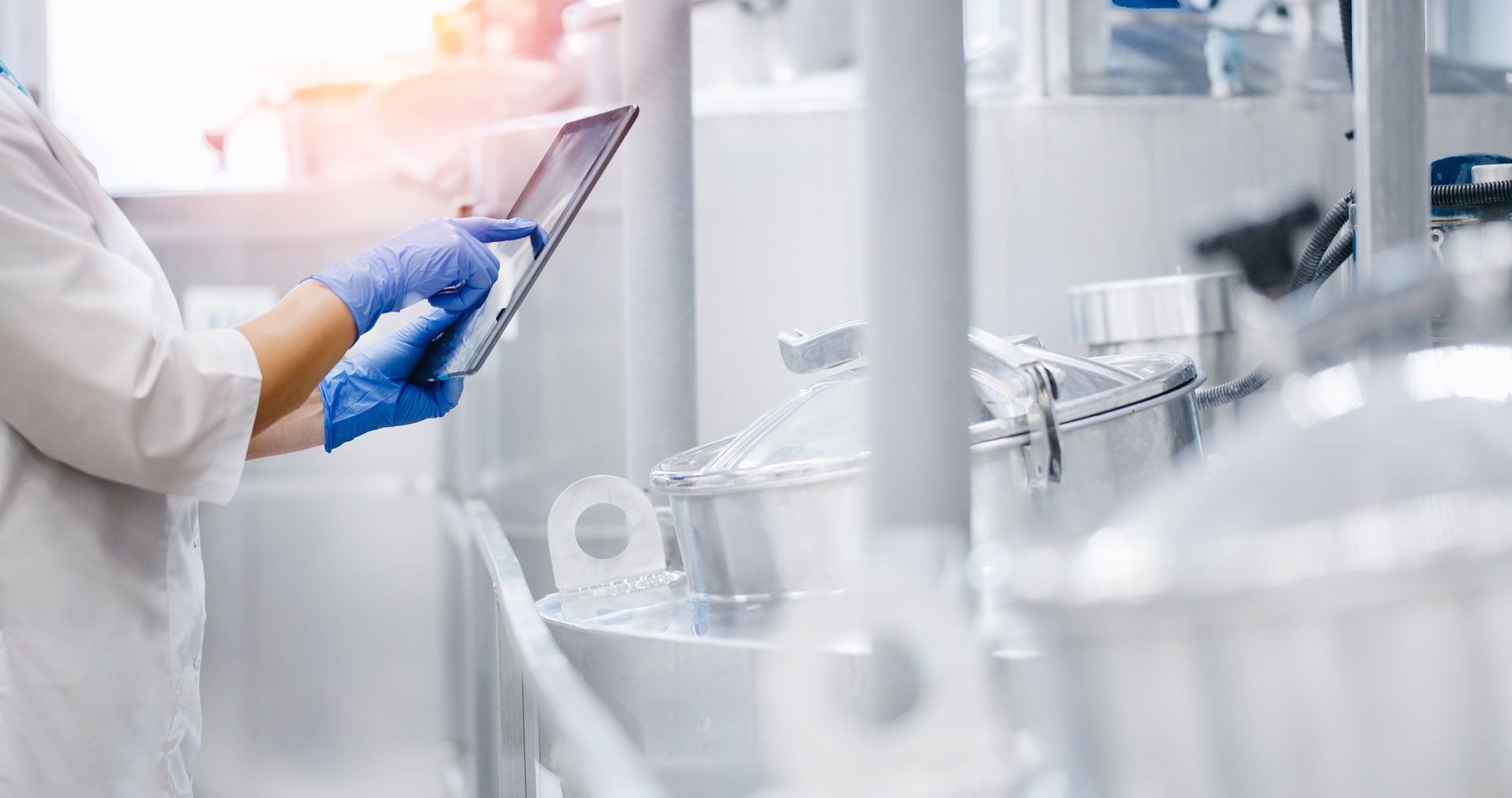
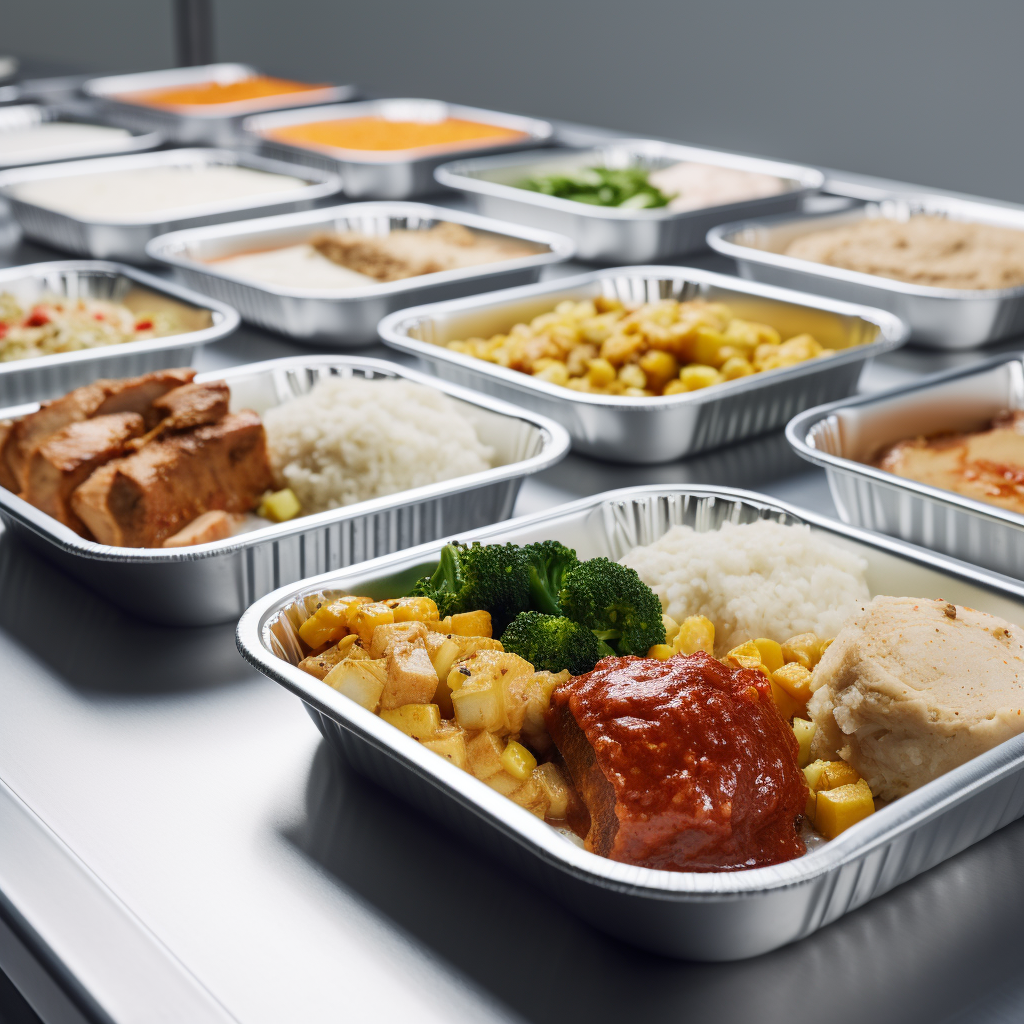