Multi-Fill’s process for food filling machine installation
Installing food filling machines, whether for a new or existing production line, is a painstaking process that requires research, planning and expertise. You cannot simply purchase whichever machine looks good and try to incorporate it into your food production line. For best results, it is advisable to work with a company that will learn about your products, examine your current setup and work with you to create a tailored solution.
Our 4-step process that’s built for you
Far from simply supplying volumetric filling machines, Multi-Fill engineers specific solutions and oversees their integration into our clients’ workflows. We take each client through a four-step process to ensure that we can get the best results.
- Step 1: Discovery: We start by visiting your plant and finding out all we need to know about your business and goals. We look at your products, study the machinery you are currently using, and devise a fitting solution.
- Step 2: Product test: Next, we bring samples of your product into our testing centers to see how well our machines work with it. This step has a dual purpose: it allows us to get a better feel for your product and the filling technology best suited to it, but it also gives you a chance to take a look at our machines and see what they can do.
- Step 3: Engineering: After the testing phase, we begin designing a solution for your production line, selecting and customizing the right filling machine for your purposes. This is the longest phase, as we take all the time we need to create the best solution. We will visit your plant again, get all the necessary measurements, get a feel for the type and size of packaging you use, generate concept drawings, and discussing your needs with you. Finally, once you sign off on our designs, we will manufacture your machines for you.
- Step 4: Installation and support: Once the machines are ready, we ship them to your plant, where our technicians will be waiting with you to complete the installation and ensure that your new, improved filling line is working correctly. We will then provide ongoing technical support to help you keep your production line running efficiently for years to come.
If you are planning on installing food filling machines, partner with
Multi-Fill. Our 4-step process will provide tailored solutions that add value to your production line.
Contact us for more information.
Designing a food filling line: Product is king

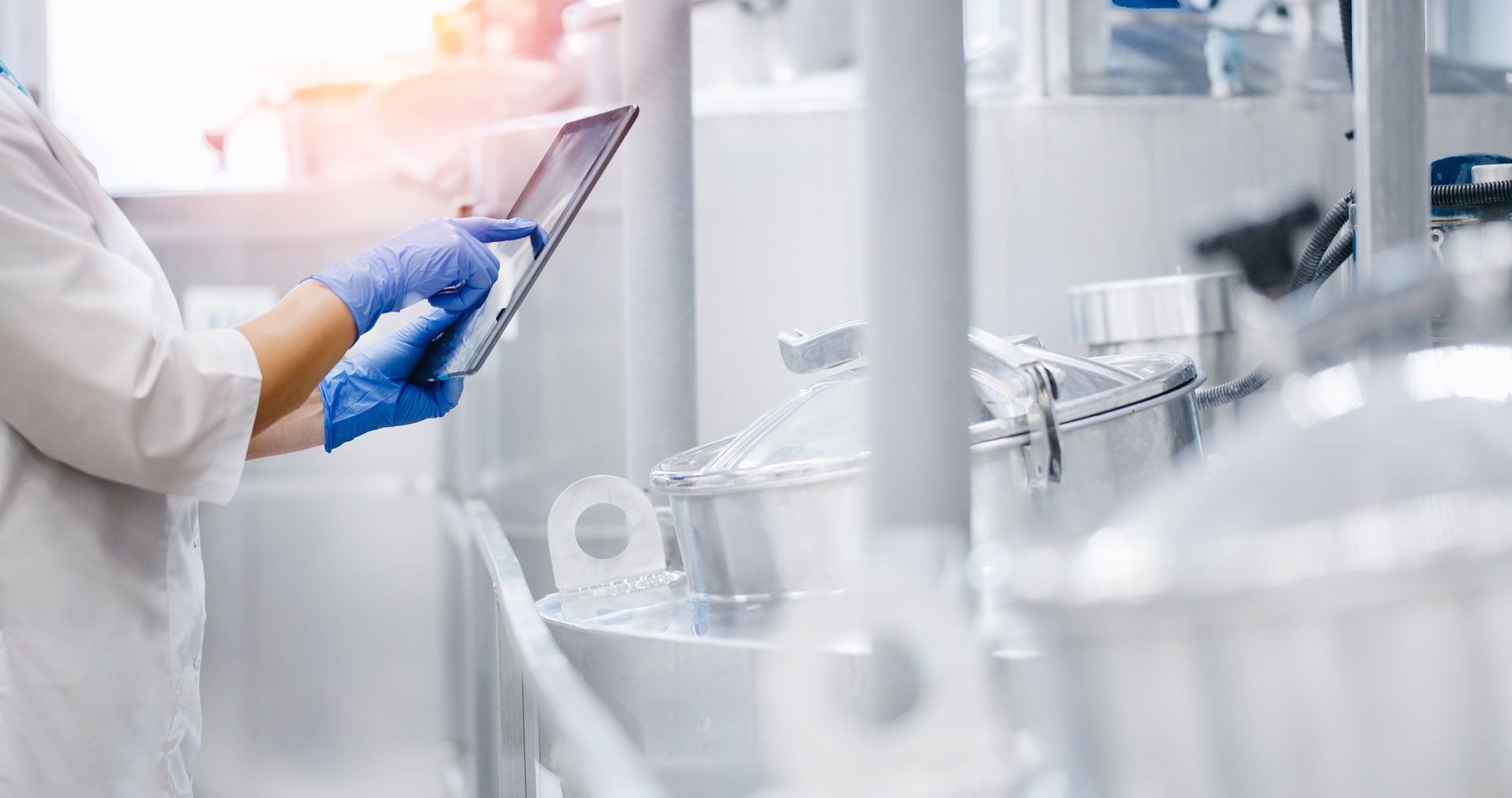
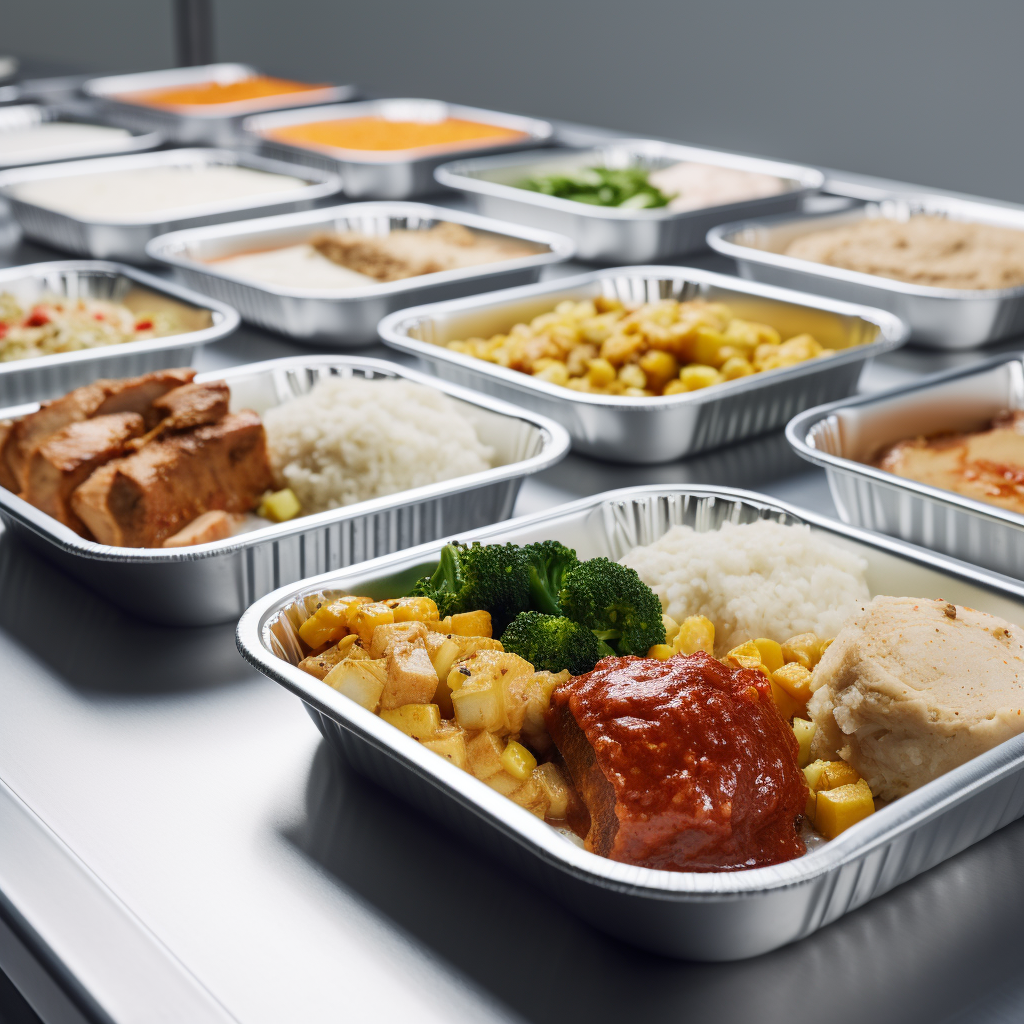