Food filling machines need to evolve to keep up with the latest consumer demands. Learn more about filling machines and their benefits.
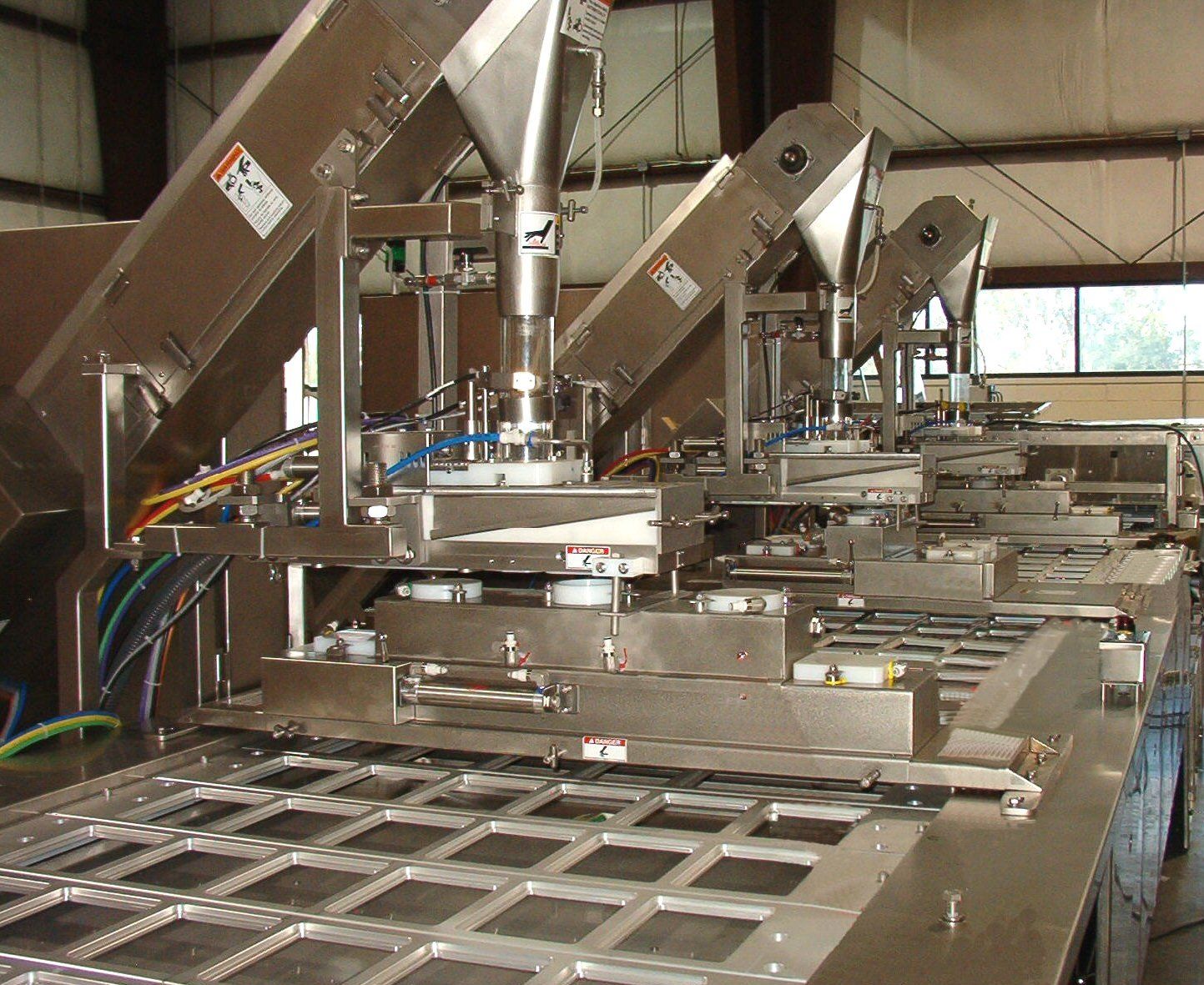
Food filling machine trends: Today's equipment is more versatile
New food filling machines are maximizing output and simplifying changeovers. Most consumers probably don’t consider the sheer volume of food products they have to choose from. The incredible differentiation of the market extends beyond the different types of food available - each with its own packaging requirements. Brand differentiation is another factor that must be considered, with manufacturers looking for packaging that reflects their brands and sets them apart from competitors. The design of food packaging, and therefore, also food filling technology, has to take both of these factors into consideration. Food grade machines need to work with this diverse array of products, while still maintaining efficiency and high output.
Designing a filling line: Product is king
When choosing a food filling machine, start by thinking about the product’s exact characteristics. Is it dry or wet, hard or soft, long, short, round or square, solid or viscous? Product specification is the starting point of filling machine selection. All product characteristics, including temperature, consistency, etc., will inform whether or not a particular machine is right for you.
Product and container versatility
These product-specific requirements suggest that a high level of specialization is required in the food packing industry. However, packing plants fill such a wide range of products, they cannot afford to purchase a specialized filling machine to fulfill each and every need. A high level of versatility is called for to improve the efficiency of a packing operation, with machines that can handle multiple products. Developers of packing technology understand this, although we have not quite reached the point of being able to provide a ‘one filler fits all’ solution. Multi-Fill’s volumetric fillers come close, with the ability to dispense hard-to-fill foods such as cooked rice and pastas, vegetables, fruit, ready-to-eat salads, sliced and shredded meats, and cereals. They can also be extremely versatile when it comes to the types of containers they can fill. These include trays, plates, cartons, cups, cans, jars, boxes and more.
Accuracy and efficiency
No food supplier should underestimate the importance of containers that are accurately and consistently filled. Under filling a container can lead to customer complaints, while overfilling is just wasteful. Accuracy is thus an essential attribute in a filling machine. Ensuring that a machine fills accurately throughout its long lifespan depends on robust design and construction that allows the machine to maintain optimal throughput with minimal maintenance.
The challenge is that a machine’s accuracy is a function of so many different internal variables. Each component in the filler’s make-up is partly responsible for maintaining accuracy and efficiency. The resulting complexity makes it difficult to keep accuracy up through manual operation, so the answer appears to be better automation. In Multi-Fill fillers, this answer to this need is found in programmable logic controllers (PLC's) that control and consistently make adjustments to the filling parameters and product flow.
Minimizing changeover time through hygienic design
When you have one machine handling a variety of products, one of the most important operational considerations is the prevention of cross-contamination. In order to prevent this, plants must perform changeover routines when switching from one product to another. These actions ensure that the machine is properly cleaned between products. The problem with changeover routines is that they take up time and thus reduce productivity. Multi-Fill has addressed the need to reduce changeover time with automatic clean-in-place (CIP) capabilities. Design factors such as minimal moving parts, tilt-out hoppers, hinged consoles, tilt-drip pans, easy head disassembly, and quick belt release, all help to facilitate easy cleaning.
Operator interaction
Even though increased automation is a universal feature of filling machine design, it is still important that equipment is easy for operators to use. Machine designers place a lot of emphasis on creating intuitive human machine interfaces (HMI) through such measures as the use of easy-to-understand pictures and signs on the machines, graphic representations or touch screens.
Food Filling Done Cost-Effectively
In addition to building filling machines that are accurate and efficient, Multi-Fill is committed to designing solutions that make good economic sense. Cost-effective filling means striking a balance between output speed and packaging quality. Our volumetric fillers deposit frozen (IQF), cooked and raw foods at speeds up to 120 containers per minute while maintaining product integrity and appearance. The list of products our machines can pack includes vegetables, pasta, rice, whole grains, pet foods, meats, fruits and more. The factors that make our machines so effective and efficient include sanitary food packing features, robust construction, easy cleaning, ease of use and flexibility.
Sanitary Filling Systems Applications
Sanitary filling systems are used in several different applications across the food and beverage industries, as well as other key sectors, such as pharmaceuticals. Although the requirement of clean and efficient filling is the same across all applications, the specifics of design and method differ substantially. Here are the three main sanitary filler applications:
Compact Filler
Compact fillers are small, portable machines that are great for businesses operating on a smaller scale or in very limited space. They generally feature a conical hopper and are available as tabletop machines or on casters for greater mobility.
Food & Beverage Filling Machines
From soft drinks to cereals and bags to bottles, there are multiple options of fillers to fit every possible packaging requirement for foods and beverages. These include baggers, bottling machines, pocket fillers and more.
Carousel filling machines
Carousel filling machines consist of circular frames with running wheels, rails and tracks. Containers are moved around the circular tracks of the filler, and filled by metered dosing devices programmed to fill each container with a precise amount.
Advantages of volume dispensers
Volume dispensers have been developed as labor- and time-saving devices for businesses that need to pack and move large quantities of food and beverage products. They have become a staple of the food industry because they offer the following advantages:
- Savings on staff and labor
- Reduced downtime
- Consistent and accurate dosing to ensure equal filling of all containers
- Automated to ensure ease of use and reliability
- Versatile - they can handle a variety of products and packaging types
- Extremely easy to clean: made of stainless steel, and feature design elements such as minimal moving parts, tilt-out hoppers, hinged consoles, tilt-drip pans, easy head disassembly, and quick belt release
Our Range of Filling Machines
Multi-Fill’s range of filling machines includes several models of volumetric fillers, with options for additions and upgrades. Our machines are compatible with a wide variety of container conveying systems, and include the following:
- MPFMP-60: A semi-automatic filler pocket filler for cooked rice and pasta, cut vegetables and fruit, cereal, ready-to-eat salads, and shredded meats. This filler is ideally suited for lower speed production lines, research and development labs, and pilot plant operations. It is rated at speeds up to 60 CPM, depending upon the product, volume to fill, container, line configuration, and operator
- MPFSH-075: An automatic pocket filler to dispense clean portions of products that are generally considered difficult to dispense, such cooked rice and pasta, shrimp and surimi.
- MPFSC-120: Dispenses clean, accurate portions of a wide variety of difficult-to-fill products
Patented Distribution Systems
Our filling machines are all designed to work with your existing conveying equipment. Our patented distribution systems help to bridge the gap between the two. They are designed to meet the challenge of depositing product doses into various line configurations. We can integrate with your specific line layout, including multi-lane conveying systems or vertical pouch machines.
Batch Feeding Hopper
The batch feeding hopper can be added to the MPFSH-075 and the MPFSC-120 machines when bulk feeding capacity is needed. It can be mounted on its own base or directly to the base of the filling machine. It can be fed by a vertical post dumper, conveyor, or chute from a second floor or platform.
Considerations when filling couscous
Couscous is a soft pasta that is known to cause problems for packing plants because it forms clumps, causing uneven distribution and sticking to machines. As a result, packing this popular food can be tricky. On the one hand, it is best to fill it as soon as possible after cooking to prevent clumping. On the other hand, it needs to cool a little so that there is no steam to form condensation in the product and make it wet. Filling a read-made couscous meal should also be done in stages with each part of the meal packed separately
How healthy eating is changing the food processing industry
Processed foods have developed a very bad reputation over the years. The bad press they have received has often been with good reason, as they have tended to contain a lot of additives, which have been proven to be unhealthy. Consumers now want healthy foods that are as whole as possible and free of additives and preservatives. However, the market for ready-made meals is booming. The challenge now is to provide meals that are healthy as well as convenient, a demand which is very possible to meet with the right ingredients and the right equipment. The latest filling machines, such as Multi-Fill’s range, can dispense the vegetables, fruits and cooked rice and pastas that form part of a good meal. All of our volumetric fillers can handle these foods, making it easy for you to pack healthy meals efficiently, cost-effectively, and attractively.
How ready-to-eat meals are changing the food packaging industry
With the rising popularity of read-to-eat meals, consumer demands in this area are also becoming more exacting. Gone are the days of simple boil-and-dump packaging. Consumers now want meals that look appetizing on the supermarket shelf. Producers now need to pack ready-to-eat food that has the appeal of freshly plated restaurant meals, while maintaining standards and keeping filling methods consistent. This requires specialized equipment, such as Multi-Fill’s semi-automated and automated volumetric fillers.
Processed quinoa and healthy eating--meeting your customer's expectations
Cooked quinoa is increasingly popular among urban eaters. Demand for this ancient grain started to grow around the year 2000 and it has increased in popularity ever since. It forms part of a variety of ready-to-eat meals; an excellent substitute for starches such as rice and pasta. Filling cooked quinoa comes with a lot of the same drawbacks as packaging cooked couscous. It is an operation that requires care and precision to prevent clumping, disturbing the flow of distribution and ending up with a high level of product variability. With the right equipment, such as Multi-Fill’s specialized filling machines, quinoa can be simple, tasty, and delicious.
Planning for spiral noodles in your factory line
Most people enjoy spiral noodles and are more than willing to buy pre-packaged meals that include them. The question, however, is how are you supposed to pack them? Cooked quinoa and couscous are tricky enough to fill. Noodles come with all the same challenges, as well as their long, spiral shape, which only makes them more inclined to clog filling machines. They are also susceptible to breaking, resulting in uneven, inconsistent and unattractive presentation. American consumers prefer noodles softer than they are generally eaten in other countries, compounding the problem. A machine that gently manages and dispenses the noodles, minimizing breakage and preventing clumping, is the solution to the problem. Multi-Fill included this specific consideration in the design of its filling machines.
Our food filling machine company’s value added services
In addition to supplying our volumetric fillers, Multi-Fill also offers a variety of value-added services. These include the following:
- Evaluation and testing of your equipment in one of our pilot plants.
- Installation and commissioning
- Machine rebuilds
- Maintenance and repairs
- Supply of spare parts
- Training
- Upgrades and modifications
Outstanding personal service is key to our relationship with our customers and involves all company departments and functions from people who know the market and challenges you face every day. We can give you fast, local decision making. Teamwork with our customers is a key to our success.
FAQs About Our Filling Machines and Services
- Are your machines wash-down? Yes. All of our machines are designed to be as sanitary and simple to clean as possible. All of our surfaces are designed with a pitch to shed water and prevent pooling. We also include full wash-down instructions with every machine.
- Can your machines do cooked or sticky rice? Yes! Sticky rice is what led to the invention of our machines. We can manage all sorts of foods, from sticky rice to pasta to fruit and more.
- How many containers per minute can you fill? The speed of our machines varies by model, layout, product to be filled, and container type. Using a distribution system, and whether it is a stop start or continuous line are other important factors. Some foods we can fill up to 120 containers per minute.
- How often do your machines need cleaning? Our machines are compliant with all applicable industry standards for cleanliness. The time between cleanings is a function of the type of product and the line speed.
- Do I need tools to clean your machines? We have designed our machines to be torn down for cleaning with no tools whatever. Assembly and disassembly is done with quick connections and hand tightening. The entire process takes only a few minutes
- Can Multi-Fill machines integrate with existing systems? Yes! Our machines are designed to be plug and play, meaning they can integrate well into virtually all existing lines. We manufacture them to fit your space and work within your existing systems.
- What is assembly and disassembly like? All of our machines are designed for ease of use and minimal training. Assembly and disassembly procedures do not require any tools whatsoever. Our machines use quick connections and hand tightening to set up and tear down.
- Where are your machines built? All of our machines are proudly built at our main factory in West Jordan, Utah, USA.
- Is Multi-Fill a good fit for me? We stand behind our products 100%, but we know our machines aren't a good fit for every product and container. Contact our team to set up a demo of your product, and see if Multi-Fill is right for your company
- Do you offer a guarantee? We work closely with your team throughout the entire engineering process to ensure our machines can handle your product, container, and production line. We build our machine specifically for your application, and we do stand behind our workmanship.
About Multi-Fill
MULTI-FILL Inc. is recognized worldwide as a leading provider of high-quality food filling systems for hard-to-fill products. Our fillers are on most ready-meal lines of the major players in the prepared foods industry as well as the smallest of customers. We have been providing volumetric filling systems to satisfied customers around the world for decades. Based in West Jordan, UT, we specialize in the production of filling systems that ease the difficulties food manufacturers experience in the packing of hard-to-fill foods such as cooked rice and pastas. Our volumetric fillers are perfectly suited for a wide range of food grade applications. Contact us today to find out how our food filling machines can fit in on your production line.
Designing a food filling line: Product is king

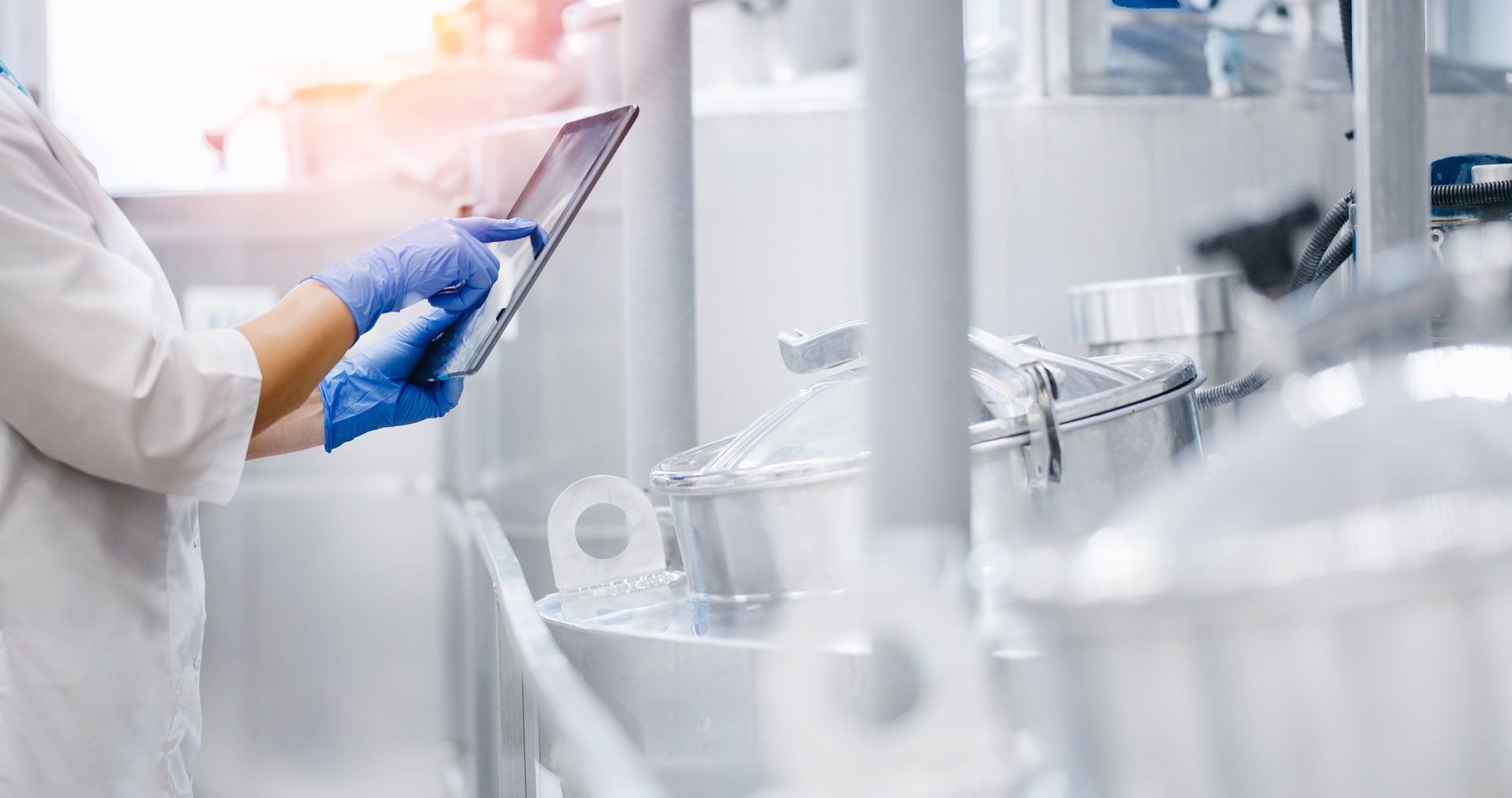
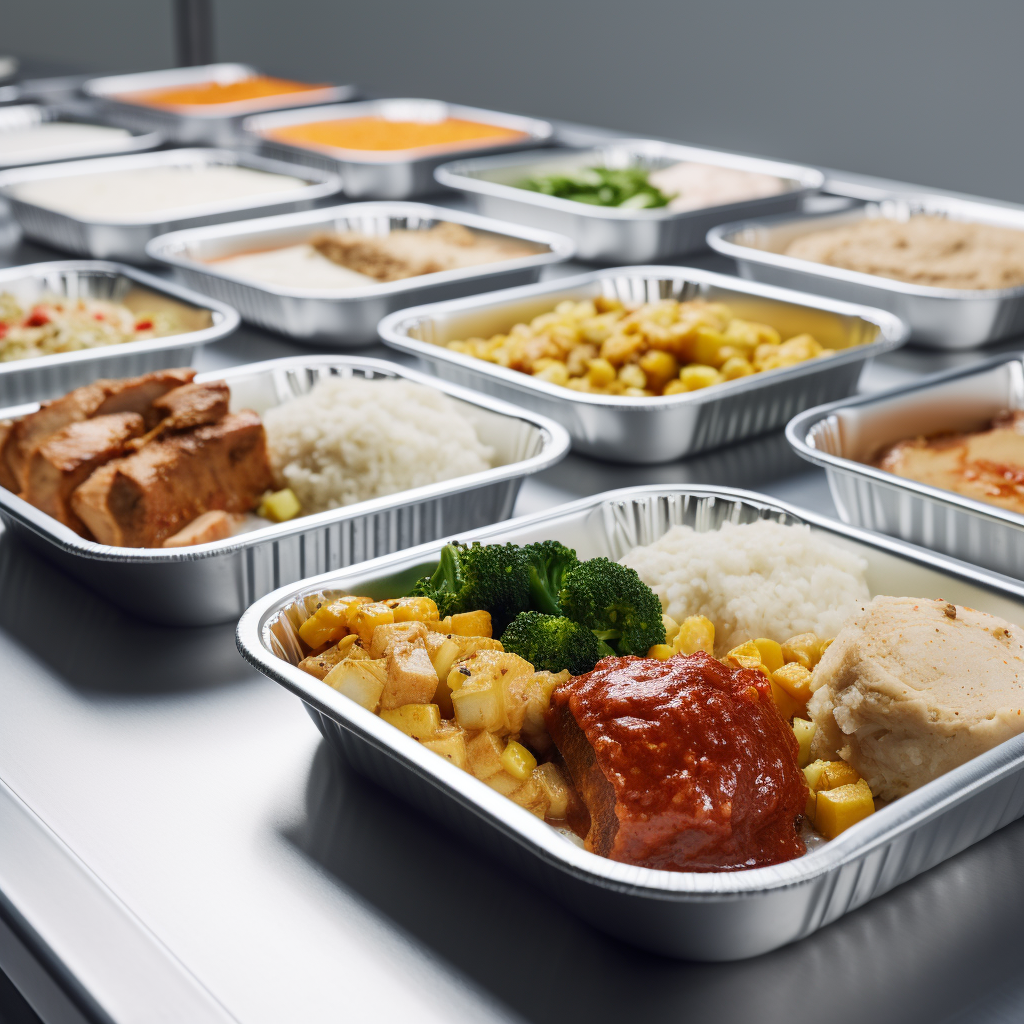