Michael Naylor • November 14, 2019
Automating your Food Factory Line
Critical Factors for a Successful Implementation
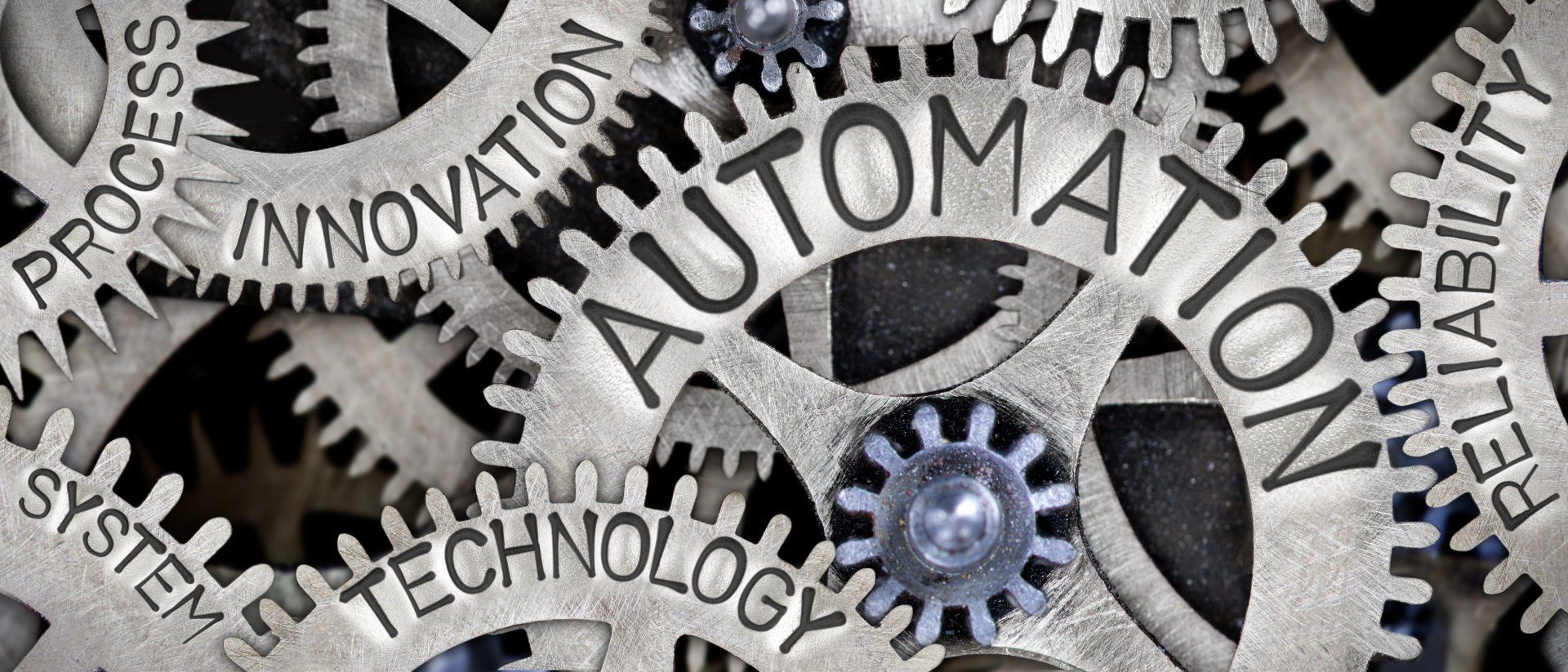
As part of a highly competitive food processing industry, you may be all too familiar with the current challenges in manufacturing, packaging and delivering quality products to customers. With rising utility costs, soaring raw material prices, and labor-intensive processes tilting your balance sheet, are you exploring the option of automating your processes?
A carefully planned and well executed automation project will help you increase production capacity, reduce long-term operating costs, and improve profitability. However, have you considered all the critical factors that go into a successful implementation?
Key Aspects to Consider While Automating a Food Factory
When you are thinking about clean, efficient production lines, and a seamless flow between processing, filling, packaging, and sealing, here are some aspects to consider:
1. Extent of Automation:
Although a start-to-end automation may be ideal, it may not offer optimum Return on Investment (ROI).
- Incremental Controls: If your current processes are largely manual, think about using incremental process control by updating the most labor intensive systems. For example, depending on your product, mechanizing processes, such as weighing, portioning, batching, or filling could offer a substantial increase in productivity, without busting your budget.
- Integrated Process: Look at tying all your equipment used in a particular process, together in an overarching system. For example, if you choose to automate the packaging process, ensure that you integrate all the individual machines and components that need to run for a fully functional packaging line. That way, if one element stops working, the entire process will not suffer.
2. Machine Selection:
The type, size, and quality of machines will depend on several factors:
- Infrastructure: Whether you are installing new machines or upgrading semi-automated lines to fully automated ones, your choice of machines will largely depend on the amount of physical space available at your site. Do you have the option to install plug-and-play models, or will you have to invest in a major overhaul that involves electrical upgrades, ducting, plumbing and such?
- Quality and Composition: Do the materials and design of the machine components favor the regulatory requirements and industry norms? For example, sub-components such as gearboxes or motors often have strengthening ribs or cooling fins on them, which could become microbiological traps or lead to pooling of stagnant water.
- Hygiene Requirements: Maintaining the highest standards of hygiene during manufacturing or packing would mean selecting machines that are easy to sanitize. If you need to dismantle the parts for washing, consider how quick or easy is it to remove and reassemble? After all, you do not want the cleaning process to eat into the hours on your next production shift.
- Production Consistency: What type of food grade oils and lubrication system greases do the machines need? Will these oils or greases impact the integrity or taste of your end product?
- Food Type: The size, shape, weight, texture, and quality of the foods you produce can significantly impact the automation of processes, such as filling or packaging. Will automated machines manipulate the requirements of your multi-product line without compromising on the product quality and line efficiencies?
3. Future Capacity Building: Does your automation plan and selection of machines consider your future production demand, potential expansion of product lines, innovation in processing techniques, or other likely changes in industry norms?
Boost Your Food Processing Line with World-Class Solutions
A strategic food factory line automation plan will help you address multiple aspects, including product quality, production speed and capacity, labor shortages, and profitability. If you are looking to automate your distribution or filling systems, explore a wide range of unique volumetric fillers
and high-speed counting machines
at Multi-Fill. With compact designs and flexible options, our filling and distribution solutions can easily integrate with both intermittent, as well as continuous motion container conveying systems. We cater to single or multiple container lanes, and horizontal or vertical bagging machines.
For affordable and efficient automated filling solutions, rely on a recognized industry leader, such as Multi-Fill. To know more about our products, call us at 801-280-1570 or contact us online.
Designing a food filling line: Product is king

Food packaging plays a vital role in ensuring the safety and quality of the food we consume. To maintain high standards and prevent foodborne illnesses, the food packaging industry follows a set of regulations known as Current Good Manufacturing Practices (cGMP). In this article, we will delve into cGMP and explore its impact on preventing foodborne illness. We will also take an inside look at how cGMP is implemented on a food factory line, the role of food filling equipment in ensuring compliance, and discuss the future of cGMP in food packaging for strengthening food safety.
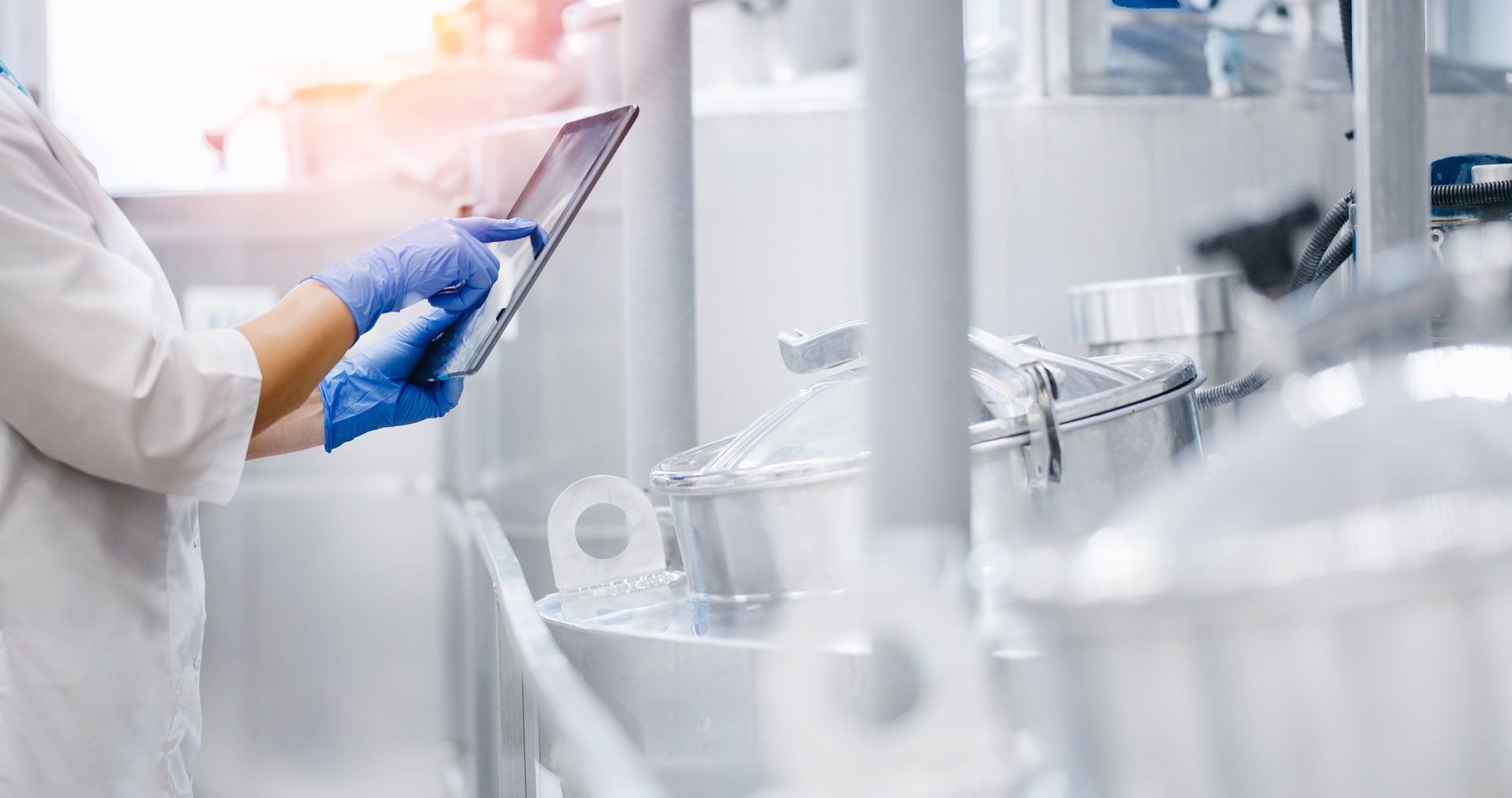
Current Good Manufacturing Practices Food safety is of utmost importance in the food industry, and several systems work together to prevent foodborne illnesses. This article explores the harmonization of Current Good Manufacturing Practices (cGMP), Hazard Analysis and Critical Control Points (HACCP), and Hazard Analysis and Risk-based Preventive Controls (HARPC) in ensuring food line safety. We will delve into the synergy between these systems, the role of critical control points, and their practical application in both automatic and manual counting devices. Additionally, we will discuss how cGMP, HACCP, and HARPC optimize automatic filling machines for enhanced food safety. This is the second in a series of articles on cGMP. Read the others here: Harnessing the Power of cGMP in Preventing Foodborne Illness: A Deep Dive into Food Line Safety Measures Delving into cGMP: Its Crucial Role in Food Packaging and Safety Decoding HARPC: Its Role in Foodborne Illness Prevention and the Importance of Critical Control Points
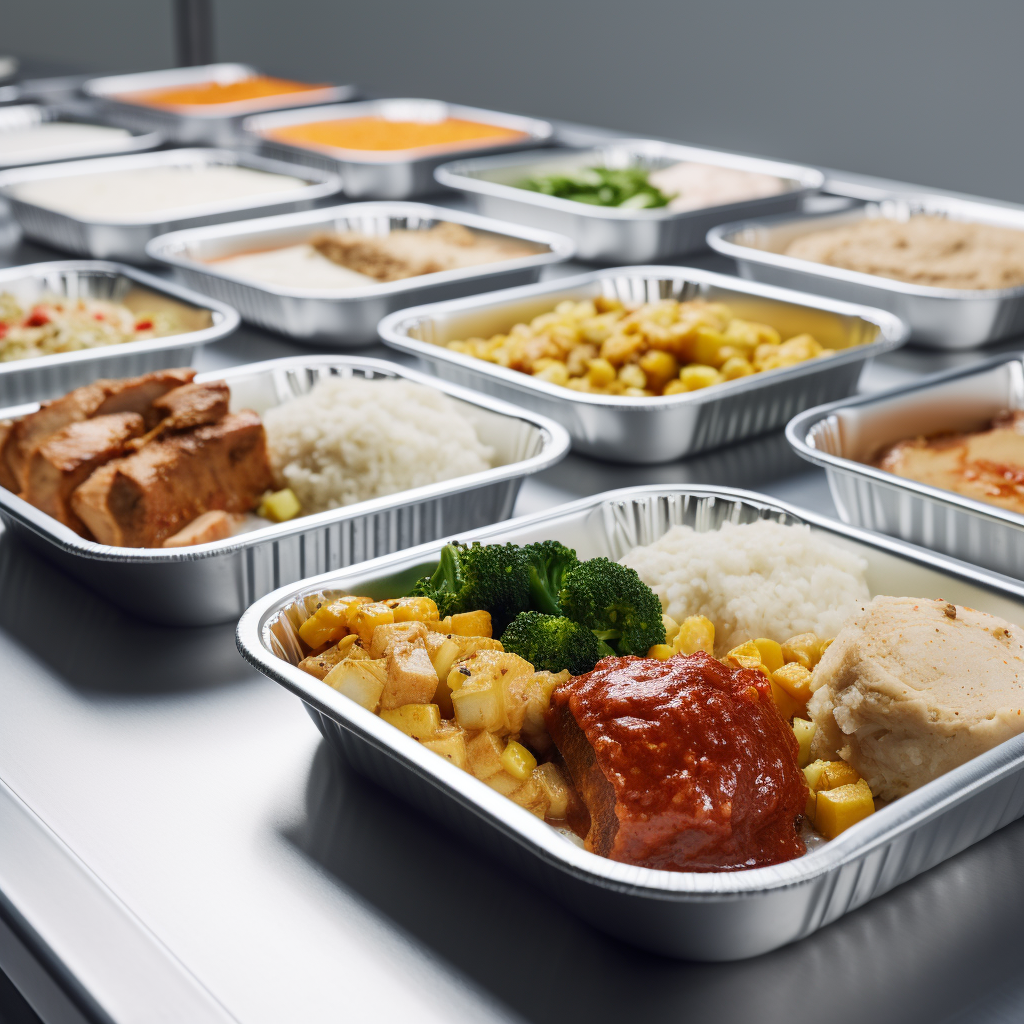
In this article, we explore the crucial role of Current Good Manufacturing Practices (cGMP) in ensuring food safety and preventing foodborne illnesses. We'll delve into the significance of hazard analysis and critical control points (HACCP) and how they contribute to mitigating risks. Additionally, we'll discuss the role of Hazard Analysis and Risk-based Preventative Controls (HARPC) in enhancing food safety measures. This is the first in a series of articles on Good Manufacturing Processes in Food Processing. In this article: Understanding the Importance of cGMP in Food Packaging How Hazard Analysis and Critical Control Points (HACCP) Prevent Foodborne Illness The Role of Hazard Analysis and Risk-based Preventative Controls (HARPC) in Food Safety Critical Control Points in Food Packaging The Intersection of cGMP, HACCP, and HARPC in Food Safety